The illusion of accuracy in analyzing plant failures
Author: M. AL MUAISUB, Saudi Aramco, Dhahran, Saudi Arabia
Plant engineers can face the illusion of accuracy in determining the responsible damage mechanism when analyzing failures or conducting incident investigations. Three things can cause the illusion of accuracy:
- The illusion of temperature limits accuracy for specific damage mechanisms. Three examples will be addressed here: graphitization, corrosion under insulation (CUI) and microbiologically influenced corrosion (MIC).
- The illusion of accuracy when depending on a single reference or industrial practice.
- The illusion of accuracy caused by confirmation bias. This is illustrated by discussing the Nelson curve development between 1967 and 2016, which is utilized to evaluate the material susceptibility to high-temperature hydrogen (H2) attack.
When reviewing American Petroleum Institute (API) Recommended Practice (RP) 571, “Damage mechanisms affecting fixed equipment in the refining industry,” it is remarkable how accurate the temperature limits are for some damage mechanisms. Take, for example, the first damage mechanism stated in the 2nd Ed. of API 571.1 The RP stipulates that graphitization is a change in the microstructure after long-term operation between 427°C and 593°C. Moreover, CUI affects externally insulated piping and equipment that operate between –12°C and 175°C for carbon and low-alloy steels and 60°C–205°C for austenitic and duplex stainless steels (SS). The final example pertains to MIC. API RP 571 states that the organisms could survive and grow at a temperature range between –17°C and 113°C. The aforementioned examples insinuate that the temperature limits seem to be very accurate.1
The question here is, “Are these numbers and limits accurate?” In other words, is carbon steel (CS) immune to graphitization after long-term exposure to 425°C since the minimum threshold is 427°C? Some industry professionals might think that CS will not suffer graphitization since the operating temperature is outside the range of this failure mechanism.
THE CAUSES OF ILLUSIONS
The illusion of temperature limits accuracy. The first cause of the illusion of accuracy in analyzing plant failures is missing the temperature scale conversion. When contemplating the three examples above with the following set of temperature ranges (as shown in TABLE 1), the perspective might become different.
Damage mechanism |
Temperature limits, °F |
Temperature limits, °C |
||
Minimum |
Maximum |
Minimum |
Maximum |
|
Graphitization |
800 |
1,100 |
427 |
593 |
CUI: CS and low-alloy steels |
10 |
350 |
–12 |
175 |
CUI: Austenitic and duplex SS |
140 |
400 |
60 |
205 |
MIC |
0 |
235 |
–17 |
113 |
TABLE 1. Temperature limits for various damage mechanisms in °F vs. °C
As observed, the temperature limits in °F illustrate a slightly different perspective than the temperature in °C. Generally, accepting a marginal tolerance of a few degrees below the 800°F limit is deemed normal. However, with the 427°C limit, such a temperature indicates a more precise value. So, back to the previous question: “Is carbon-steel microstructure immune to graphitization after long-term exposure to 425°C since the minimum threshold is 427°C? The answer is no, and here is why. One of the most interesting issues in the April 2020 revision of API RB 571 is that the minimum and maximum temperature limits of graphitization were changed to 425°C and 595°C, respectively. Moreover, the same goes for MIC—the minimum temperature was decreased by 2°C, and the maximum temperature was increased by 2°C. Such changes were only reflected in the stipulated temperature in °C.2 However, for °F values, the temperature limits remain the same. Such conflicting viewpoints for the same scenario could cause the illusion of accuracy.
The illusion of single reference accuracy. Industry professionals should manage temperature limits with diligence to avoid falling into the second illusion of accuracy. For CUI, such temperature values are not recognized in all industry codes and recommended practices. API RP 583, “Corrosion under insulation and fireproofing,” stipulates the following: “In many cases, such as ammonia terminals, piping temperatures can swing from ambient to –30°F (–27°C) during periods when ammonia is flowing in the piping. This temperature swing leads to continuous freezing and thawing, and results in wet conditions that increase piping system susceptibility to CUI damage.”3
Although the process temperature is –30°F (–27°C) (i.e., lower than the minimum limit in API RP 571), CUI can develop in the process piping underneath the insulation due to intermittent operation. Moreover, when comparing the 1st and 2nd Ed. of API 571, it is noticed that the 1st Ed. did not specify temperature limits. In contrast, the 2nd Ed. breaks down the limits based on the type of material: carbon and low-alloy steels vs. austenitic and duplex SS.1,4 Although the evolution in understanding a damage mechanism is expected, the dependence on a single industrial practice or even an older version of a document could negatively impact the investigation. Therefore, determining the responsible damage mechanism based on a single value (i.e., the specified operating temperature) and ignoring the intermittent operation and temperature trends in the process might detour the investigation to incorrect conclusions.
This illusion of accuracy could be revealed in a single document through multiple editions. It is worth reporting another critical change between the 2nd and 3rd Ed. of API 571 [i.e., the temperature limits of CUI (see TABLE 2)]. First, the 400 series SS was not part of the affected materials in the 2nd Ed. and was included in the latest revision. Another critical change is lowering the maximum temperature limit for CUI in austenitic and duplex SS materials by 50°F and increasing the minimum temperature limit for duplex SS by 140°F. Such changes should be reflected in relevant industrial documents and systems such as risk-based inspection reports, corrosion control documents and other monitoring systems based on the integrity operating window to ensure plant integrity. Nevertheless, highlighting these changes should warn failure analysts and corrosion engineers to avoid the illusion of accuracy due to the reliance on a set of numbers that are prone to changes.2
CUI |
2nd Ed. (April 2011) |
3rd Ed. (March 2020) |
||
Minimum |
Maximum |
Minimum |
Maximum |
|
CS and low-alloy steels |
10°F (–12°C) |
350°F (175°C) |
No change |
|
400 series SS |
Not included in affected materials |
10°F (–12°C) |
350°F (175°C) |
|
300 series SS |
140°F (60°C) |
400°F (205°C) |
No change |
350°F (175°C) |
Duplex SS |
140°F (60°C) |
400°F (205°C) |
280°F (140°C) |
350°F (175°C) |
TABLE 2. Temperature limits for CUI in different materials1,2
Another example of this illusion can be illustrated through MIC. Going back to the listed temperature limits in TABLE 1, it is clear that a wide range of temperatures could allow MIC to attack the material. However, other references like the NACE Corrosion Engineer’s Reference Guide5 delve into details about which bacteria attack which material under what temperature and pH ranges. To clarify, a detailed table in the NACE book titled, “Microorganisms commonly implicated in biological corrosion,” lists the type of bacteria that attacks iron and steel alloys. It states that the minimum and maximum temperature limits are 10°C and 40°C, respectively. Therefore, when analyzing a pipe failure where the water is near boiling temperature, it might be challenging to assume that MIC is the culprit based on the temperature limits stipulated in API 571.
The illusion of accuracy caused by confirmation bias. Besides the temperature scale conversion and the different temperature limits between the recommended practices, confirmation bias can lead to the illusion of accuracy. Confirmation bias tends to locate evidence to support an idea or hypothesis while disregarding other contributing factors. This bias can significantly mislead industry professionals, especially during failure investigations. To overcome this misconception, the failure investigator should not ignore the least likely cause of failure, even if the operating parameters might reside outside the specified envelope for a damage mechanism. An excellent example is detailed in the following paragraph to illustrate this cause of the illusion of accuracy based on a high-temperature H2 attack (HTHA) and the Nelson Curve specified in API 941.
Example. In 1967, G. A. Nelson developed his famous figure, which specifies the various grades of steels and the safe operating limits of temperature and H2 partial pressure to avoid HTHA. However, the figure was revised by API in 1969, 1983, 1990, 1996 and 2015. Such revisions were conducted due to various incidents with C-0.5Mo steels, which reduced confidence in the accuracy of the 0.5Mo steel curve. So, in 1977, the 0.5Mo steel curve was lowered by approximately 60°F (33°C) to reflect several plant experiences that involved damage by HTHA in equipment made from this type of steel. Nevertheless, in 1990, the 0.5Mo steel curve was removed from the Nelson Curve due to multiple cases of HTHA of steel equipment occurring by as much as 200°F (111°C) below the curve.6 Therefore, in some instances, it is acceptable to challenge the specified limits for a critical factor of a recognized damage mechanism in the industry.
Takeaway. This article has discussed three illusions of accuracy: the illusion of temperature limits accuracy, the illusion of single reference accuracy and the illusion of accuracy caused by confirmation bias. It is essential to recognize the adverse effects of such illusions of accuracy during the failure investigation process to avoid rolling out potential damage mechanisms. Moreover, engineers, scientists, industry professionals and academia should test these critical factor thresholds for various damage mechanisms. It is possible that a failure under investigation could result in a new exception or the revision of a threshold of a known damage mechanism, especially if it is related to metallurgical or corrosion failures.
LITERATURE CITED
1 API RP 571, “Damage mechanisms affecting fixed equipment in the refining industry,” 2nd Ed., American Petroleum Institute, April 2011.
2 API RP 571, “Damage mechanisms affecting fixed equipment in the refining industry,” 3rd Ed., American Petroleum Institute, March 2020.
3 API RP 583, “Corrosion under insulation and fireproofing,” American Petroleum Institute, 2014.
4 API RP 571, “Damage mechanisms affecting fixed equipment in the refining industry,” 1st Ed., American Petroleum Institute, December 2003.
5 Baboian, R. and R. Treseder, NACE Corrosion Engineer’s Reference Book, NACE, Houston, Texas, 2002.
6 API RP 941, “Steels for hydrogen service at elevated temperatures and pressures in petroleum refineries and petrochemical plants,” 8th Ed., American Petroleum Institute, 2016.
ABOUT THE AUTHOR
Mohammed Al Muaisub is a Senior Materials Engineer and a certified Root Cause Analysis (RCA) professional working in the Consulting Services Department for Saudi Aramco. He has 17 yr of experience working in various engineering roles in the oil and gas and petrochemical industries. Al Muaisub has led several failure investigations related to mechanical, metallurgical and corrosion damage mechanisms in pipes and static and rotating equipment. He is a certified refining corrosion technologist from NACE and a certified failure analysis engineer from ASM international. He holds an MS degree in materials engineering from the University of British Columbia in Vancouver, Canada, and a BS degree in mechanical engineering from KFUPM.
Related News
Related News
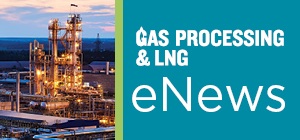
- Woodfibre LNG receives BCEAO order to move floatel to site to house non-local workforce
- QatarEnergy, Exxon seek to remove contractor from Texas gas project
- Veolia, Waga Energy and ENGIE collaborate to develop renewable natural gas industry in France
- Congo Brazzaville becomes an LNG exporting country
- Fulcrum LNG to pair with McDermott, Baker Hughes for Guyana gas project
- EU approves law to hit gas imports with methane emissions limit
- Veolia, Waga Energy and ENGIE collaborate to develop renewable natural gas industry in France
- Hawai'i Gas selects Eurus Energy America, Bana Pacific for hydrogen and renewable natural gas projects
- TotalEnergies increases LNG deliveries to Asia with two new contracts
- Desert Mountain Energy Corp. initiates helium production
Comments