Digital Exclusive: The value of experience—Why expertise matters in compressor overhauls and revamps
M. SMITH, Burckhardt Compression (U.S.) Inc., Waller, Texas
It is no exaggeration to say that without compressors, countless industries ranging from petrochemicals to brewing would grind to an almost instant halt. For the companies working in these sectors, it is critical to ensure their equipment is working efficiently and reliably.
Over time, many businesses face challenges when working with the original equipment manufacturer (OEM) of their compressors. Whether due to poor service, the age of the equipment or a loss of connection with the OEM, companies often seek alternatives for repair and maintenance. However, this move can come with risks of its own, as there is no guarantee that a third party can offer the same level of performance (FIG. 1).
FIG. 1. Working with a partner that can handle third-party compressors but also brings extensive experience and comprehensive engineering expertise to the table can help businesses face challenges when working with the original equipment manufacturer (OEM) of their compressors.
Fortunately, a third option exists: working with a partner that can handle third-party compressors but also brings extensive experience and comprehensive engineering expertise to the table.
These companies’ expertise in compressors—whether their own or those from other brands—positions them as an invaluable partner for complex overhauls and revamps. Using their in-depth understanding of compressor systems and decades of engineering experience, these businesses can often deliver solutions that go beyond what a compressor’s actual OEM can offer.
The need for an experienced partner. There are many potential reasons why businesses find themselves unable or unwilling to continue working with the OEM of their compressors.
In some cases, a particular OEM might not provide the level of service or support the customer requires. In others, the compressor may be so old that the OEM no longer holds the necessary documentation or carries the replacement parts. Occasionally, the issue is that working with the OEM is simply impossible because the business that manufactured the compressor no longer exists.
Regardless, this situation can leave operators in a difficult position, facing costly downtime or equipment replacement when they encounter issues with the compressor.
Experience and engineering expertise come into play here. A partner with comprehensive engineering expertise can step in to offer comprehensive maintenance, repair and revamp services (FIG. 2). Even if the compressor was built by another manufacturer, a highly skilled, highly experienced engineering team can almost always find a way to deliver a solution that restores the equipment to peak performance. Often, they can even exceed the quality of service provided by the OEM.
FIG. 2. Even if the compressor was built by another manufacturer, a highly skilled, highly experienced engineering team can almost always find a way to deliver a solution that restores the equipment to peak performance, often exceeding the quality of service provided by the OEM.
The author’s company is more than capable of taking on the challenge of working with other brands’ equipment, and has extensive experience with these kinds of projects.
Example 1: Overhauling a compressor for better service. At a Swiss refinery, a compressor that was essential to operations was experiencing reduced efficiency and reliability. The refinery needed a service provider that could address these issues and ensure ongoing reliability. While the compressor was not one of the author’s company’s, the company was engaged to assess and restore the equipment.
The engineering team conducted a detailed analysis of the compressor, identifying areas where previous repairs had fallen short. Through a systematic overhaul, the compressor was brought back to full operational status, ensuring that the refinery could continue its operations with minimal disruption. The revamp process included replacing worn components, restoring tolerances and re-establishing performance levels that met operational requirements.
Example 2: Reviving a 27-yr-old compressor at an Indian refinery. In India, a refinery had been using compressors that were > 27 yr old. These compressors had long since been unsupported by the OEM, and the lack of available technical documentation or OEM guidance posed a significant challenge. Despite these obstacles, the compressors were critical to the refinery’s operations, and a revamp was necessary to ensure continued performance.
The author’s company’s engineers used their expertise to reverse-engineer the compressors. With no original blueprints, they recreated the necessary tolerances and specifications. This process included measuring and assessing each part of the compressors to develop new technical drawings and ensure the revamp would meet performance standards. The compressors were then thoroughly refurbished to extend their operational life and reliability.
Example 3: Zero-hour revamp of a U.S. gas plant’s second-hand compressors. A gas processing company in the U.S. faced the challenge of high rental costs for compressors at a remote location. To reduce expenses, the company acquired two second-hand compressor packages, each from different manufacturers, with the goal of revamping them to zero-hour standards.
The author’s company managed the full scope of the project, addressing logistical challenges posed by the remote location and overseeing every aspect of the revamp process. This included coordinating the transport of the equipment, setting up cranes for heavy lifting and conducting a complete overhaul of the compressors and their engines. The compressors were brought back to zero-hour standards, ensuring they would operate as efficiently and reliably as new units. The overhaul involved not only the restoration of the core mechanical components, but also the integration of upgraded parts to improve performance and reduce the need for future maintenance.
The value of experience. The ability to overhaul and revamp compressors shows the tangible value of comprehensive engineering expertise. Experience brings an in-depth understanding of equipment design, access to high-quality replacement parts and the ability to apply advanced engineering techniques to complex machinery. This combination ensures that even older or non-standard compressors can be restored to optimal performance.
For industries where compressor reliability is critical to maintaining productivity, working with a partner that has decades of in-depth engineering knowledge is invaluable. Whether the issue stems from aging equipment, inadequate support or a complete lack of documentation, a qualified engineering partner can step in to deliver tailored solutions. These experts can navigate challenges like reverse engineering parts, diagnosing performance issues and restoring equipment to zero-hour standards.
A proven track-record of successful overhauls and revamps demonstrates the tangible benefits of this expertise. By minimizing downtime, extending the lifespan of equipment and ensuring efficiency, an experienced partner plays a critical role in smooth and profitable industrial operations. Companies that prioritize working with experienced providers can avoid costly disruptions, improve the reliability of their assets and extend the life of key equipment, ultimately improving the long-term success of their operations.
ABOUT THE AUTHOR
Michael Smith is a Shop Manager for the Services Division of Burckhardt Compression (US) Inc., in Waller, Texas. He also represents the Burckhardt Compression Worldwide Service Center for their Green Stream Parts Repairs for North America. Burckhardt Compression, a Swiss company, creates leading compression solutions for a sustainable energy future. Smith has a stellar background in all things related to machines, shops and operations. After graduating from Lone Star College with a degree is machining technology, he started working as a machinist in 2000 at a leading oil field production facility. He worked his way up through the ranks as a conventional machinist, CNC machinist, programmer, foreman and manager. Smith currently leads an incredible shop team.
Related News
Related News
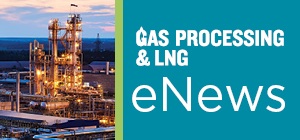
- Biogas in France: TotalEnergies starts its 2nd largest unit in Normandy
- Parker Hannifin joins iHAPC project to test H2 and argon for cleaner and more energy-efficient engine technologies
- Digital Exclusive: The future of gas turbines in the green revolution
- LNG retrofits surge as maritime industry seeks short-term carbon reduction solutions
- Kent secures integral role in engineering and execution of Wormington compressor station project
Comments