UGS installs biogas upgrading system in Michigan and Wisconsin (U.S.)
Unconventional Gas Solutions (UGS) announced the successful commissioning of two innovative biogas upgrading plants in the U.S. states of Michigan and Wisconsin. The two plants, which together feed 800 Nm3/hr of biomethane into the local gas grid, are the first UGS systems of their kind. The two projects exemplify the company's commitment to developing innovative and sustainable gas upgrading systems and offering economical solutions even under unusual conditions. The projects were particularly challenging due to the change in operating procedures and the high grid requirements. The first commissioning, the Three Petals RNG plant in Berlin, Wisconsin, was followed by the second: the Red Leaf RNG plant at the Maple Row Dairy Farm in Saranac, Michigan.
In cooperation with the project developer Novilla RNG, UGS played a decisive role in the development, commissioning and optimization of the systems. The specialist is thus setting a new benchmark in the treatment of biogas: when high H2S concentrations occur, operators normally have to pre-treat the biogas with costly additives or install an expensive external desulphurization system for the entire biogas volume. This reduces the H2S load to levels that can be handled by an activated carbon filter. However, this approach is often accompanied by a decisive disadvantage: The need for such systems to increase oxygen addition; the additional oxygen can also affect the product gas quality. At the sites in Berlin and Saranac, however, those responsible decided to bypass this complex process.
Decision in favor of UGS. Both plants process H2S concentrations of more than 4,000 ppm, which are sent directly into the compressor of the gas treatment plant and then directly through the first membrane stage. Instead of focusing on protecting the membrane treatment system, Novilla and UGS opted for an unconventional approach: the system uses a multi-stage, membrane-based treatment process that tolerates very high H2S concentrations of up to 30,000 ppm.
No expensive H2S pre-treatment required. In the first membrane stage, H2S and CO2 are separated simultaneously and fed into the exhaust gas. This means that no upstream costly process is required to reduce the H2S load. For optimum methane yield, the permeate from the subsequent stage is fed back into the process. The result is almost pure biomethane in natural gas quality with only a residual H2S content. The low concentration in the reduced volume flow on the product gas side is then separated in a fine desulphurization process using an iron sponge reaction bed. Similar to the known activated carbon filters, these vessels are arranged in a lead-lag configuration. This allows the loaded material to be renewed during operation. Another positive side effect of this H2S-binding reaction is the consumption of residual oxygen. The by-product of the reaction is water, which must be removed using a TSA dryer system developed by UGS. Ultimately, this process reduces the volume of gas to be cleaned of H2S and avoids the accumulation of O2 or N2, as would be necessary with upstream H2S treatment.
Strict grid requirements in Michigan. Another argument in favor of the selected system in the Red Leaf RNG plant was the strict grid requirements in Michigan, where an O2 content of 5 ppm must not be exceeded. In order to guarantee these extreme limit values in every situation, the catalytic deoxidation system (De-Oxo) developed by UGS was installed after the fine desulphurization of the product gas. “Remarkably, the desulphurization via the membrane unit itself, followed by the fine desulphurization on the product gas side, means that the grid specifications can sometimes even be met without using the De-Oxo system. However, the DeOxo system offers absolute safety for all our sites”, emphasizes Mark Hill, Co-CEO of Novilla RNG. This is because the oxygen remaining in the product gas is consumed in the reaction beds of the fine desulphurization system during the reaction of H2S to Fe2S3, so that the limit value of 5 ppm can be met even without the DeOxo unit installed.
Bundling technical advances at one location. For UGS, these projects represent a milestone because they combine several technical advances developed in recent years with proven results. This is particularly true in light of the fact that the biogas market is not only developing rapidly in the USA, but also in Europe. The German biogas market provides a good example. While the population of biogas plants in Europe has risen significantly in recent years to over 19,000 plants, 60% are in Germany alone. There, the considerable subsidies provided between 2004 and 2011 initially favored the production of biogas from energy crops for use in combined heat and power generation. With the incentive systems for biogas production based on energy crops, the technologies have become as standardized as the energy crops themselves – until now.
Overcoming complex technological challenges. The new pricing systems that valorize biomethane produced from manure and waste have contributed to the reduction of CO2 emissions and have significantly changed biogas qualities. Today, biogas upgrading plants must be able to cope with significant fluctuations in gas composition, large amounts of pollutants such as H2S above 5,000 ppm and changing O2 and N2 concentrations. These developments are forcing the industry to develop new solutions. Due to its high level of expertise in unconventional gas purification, UGS is in a position to technologically overcome these complex challenges: “We have innovative solutions that can fill critical niches in this market. UGS offers systems manufactured both in the USA and in Europe, ensuring innovative solutions for the upcoming market requirements,” emphasizes Ben Bikson, CTO of UGS LLC. Ben Bikson is one of the founders of the commercial gas separation membrane field and holds more than 70 granted US Patents in the membrane field.
Related News
Related News
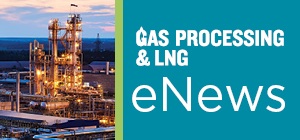
- Biogas in France: TotalEnergies starts its 2nd largest unit in Normandy
- Parker Hannifin joins iHAPC project to test H2 and argon for cleaner and more energy-efficient engine technologies
- Ukraine plans to import 800 MMm3 of gas until April after Russian strikes
- Digital Exclusive: The future of gas turbines in the green revolution
- LNG retrofits surge as maritime industry seeks short-term carbon reduction solutions
Comments