Sponsored Content: The role of natural gas and LNG in the world today
Thorbjoern Fors is the Executive Vice President of Siemens Energy’s Industrial Applications division. Prior to this position, he served as CEO of the Service Distribution Generation and Oil and Gas business unit of Siemens. He also held EVP roles in the organization’s industrial power generation and compression business and within global marketing and sales of new equipment. Mr. Fors is a mechanical engineer with more than 25 years of international experience in business development, sales, operations, and leading global businesses.
Q: What is your take on the role of natural gas and LNG in the world today, and how will it evolve as the Energy Transition progresses?
TF: I think the last few months have shown us just how important natural gas and LNG are to global energy security. There is no question we must do more in the coming years to accelerate the build-out of renewables, including wind, solar, and hydrogen; however, the transition cannot happen overnight. In the interim, natural gas can serve as a reliable bridge fuel and a replacement for coal, which still accounts for more than one-third of power generation globally. As an industry, we do need to look harder at how we can reduce emissions across the natural gas value chain. Decarbonization of LNG infrastructure is an essential part of that and one that we are intently focused on at Siemens Energy.
Q: On the topic of decarbonization, what steps are you seeing the LNG industry take to reduce its carbon footprint?
TF: The extent to which an LNG facility can reduce its carbon footprint has become a critical competitive advantage. This was not the case just a few years ago. Fortunately, the industry is making progress on improving sustainability and incrementally reducing emissions. Electrification (i.e., eLNG) has emerged as a powerful decarbonization pathway and will continue to become more attractive as the share of renewables in the energy mix grows.
In addition to all-electric liquefaction trains, we are also seeing growing interest in other technologies from customers, many of which are well-established in industrial applications like hybrid/dual drives, heat pumps, energy storage, and systems for capturing fugitive emissions – to name a few. In addition, hydrogen-capable gas turbines and carbon capture are considered novel concepts for the industry but are also gaining traction as enablers of deep decarbonization.
Q: Siemens Energy was awarded a significant contract for the Woodfibre eLNG project in Canada. Can you talk about what Siemens Energy is providing and why the facility will be unique?
TF: Siemens Energy is the single solution supplier for the all-electric Woodfibre project.
Our scope of supply includes all equipment associated with the main refrigeration trains, including compressors, synchronous motors, variable speed drives, converter transformers, harmonic filters, and numerous powerhouses. The facility will be sized for 2.1 million tonnes per annum (MTPA) and utilize clean, renewable hydroelectricity – making it the world’s lowest emission LNG facility.
The project is significant regarding its global decarbonization implications because most of the LNG produced will be exported to Asian economies, which rely heavily on coal for power generation. We are proud to be playing such an essential role in the project’s development and believe it serves as a salient example of what is possible when there is close collaboration between various project stakeholders, including operators, EPCs, and OEMs.
Q: Are there any steps or measures you think the industry can take to streamline the development of eLNG plants and improve the likelihood of projects reaching final investment decision (FID)?
TF: The development of eLNG facilities often presents unique technical challenges not encountered with traditional gas turbine-driven designs. This is particularly the case for plants that use (or have plans to use) the external grid as their primary source of power.
Even with highly stable grids, steps must be taken to avoid voltage dips while maintaining a stable frequency under all scenarios. Complexity is often amplified due to significant harmonic sources in the system caused by the large electrical motors and drives. The potential incorporation of intermittent renewables in the future is another factor operators must consider when designing the plant’s electrical system.
To this end, evaluating the liquefaction trains while predicting the feedback from the electrical distribution system is of critical importance. eLNG facilities, which have their own source of power generation, can present similar challenges. Traditionally, the parties involved with designing and engineering the liquefaction island, the electrical system, and the power plant have operated in silos, with different mindsets and objectives. We believe this needs to change for the industry to succeed in the coming years.
Q: What about digitalization; how can that be leveraged, particularly in the context of plant decarbonization?
TF: The value that can be realized through digitalization is no longer hypothetical. There are many examples where it has generated quantifiable benefits for LNG plant operators, including reduced OPEX, improved uptime, and a lower carbon footprint.
A substantial portion of emissions in an LNG plant are generated from venting and de-inventory during start-up, shutdown, and maintenance. The use of digital technologies for monitoring and analysis can contribute to a reduction in these activities by enhancing overall equipment availability and optimizing maintenance cycles.
Today, there are a host of technologies in the available toolbox of an LNG plant – from advanced data analytics based on artificial intelligence, to remote diagnostic services for gas turbines, to full-scale digital twins of compressor trains. However, when it comes to reducing emissions, the goal for operators should be to apply these solutions in ways that maximize return on investment and facilitate harmonization of the entire LNG production process.
Q: You have spoken in past interviews about the importance of collaboration between companies when navigating the Energy Transition. How does that apply to the LNG industry?
TF: Achieving net-zero emissions or anything close to it is not something any single company can do on its own. Long-term partnerships are needed across the LNG value chain to drive decarbonization and expand the range of business cases for emerging technologies like CCUS and hydrogen. Operators possess the engineering and project management expertise to drive successful LNG developments. However, minimizing a facility's carbon footprint over its life requires a holistic approach with collaboration between stakeholders early in the project lifecycle.
The government also has a vital role to play by instituting policies and regulations that foster green technology adoption and, in turn, the build-out of sustainable LNG infrastructure. Everyone’s resources and expertise will have to be brought to bear to improve sustainability, reduce costs, and ensure long-term success. At Siemens Energy, this is something we not only believe but are putting into practice today with our partners and customers.
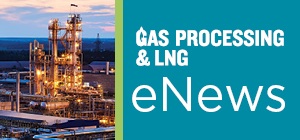
- Gasum powers Equinor's platform supply vessel with bio-LNG
- Oman plans third LNG train, boosting domestic production to more than 15 MMtpy
- ADNOC deploys pioneering AI-enabled process optimization technology
- Mexico Pacific announces long-term LNG SPA with POSCO International
- ONEOK to acquire Medallion and controlling interest in EnLink for $5.9 B
Comments