GPA Europe '19: Novatek records great achievements with Yamal LNG project
By Adrienne Blume, Editor, Gas Processing & LNG and Executive Editor, Hydrocarbon Processing
AMSTERDAM—On the afternoon of Day 1 of the GPA Europe Spring Conference, Christian Bladanet of TechnipFMC spoke to attendees about the execution and achievements of the Yamal LNG export project in Russia.
Private Russian firm Novatek commissioned its Yamal LNG project in 2017 after taking FID in early 2013. Full production was achieved in December 2018. The terminal comprises three LNG trains of 5.5 MMtpy each, and is 50.1% owned by Novatek, 20% held by Total, 20% owned by China National Petroleum Corp. and 9.9% held by China's Silk Road Fund.
An icy challenge. The average winter temperature at the project site is –10°C, and the minimum temperature is around –50°C. The sea is frozen nearly nine months of the year. Although LNG liquefaction is a cryogenic operation, some parts of the LNG plant do not operate at cryogenic temperatures, Bladanet explained.
To solve this challenge, 1,850 km of heating cables, 3,000 electrical heat tracing circuits and 46,000 junction boxes were installed at the plant, and 41 MW of absorbed power is utilized—roughly the power of one gas turbine.
Another interesting design concept, Bladanet said, is that the Yamal plant is built on permafrost. Thermosyphon heat pipes were installed onsite to avoid melting of the permafrost.
Custom process design. The site also features a complex, first-of-a-kind refrigerant compressor configuration. Instead of having two compressors in series, all the services were placed on the same shaft, with two shafts in parallel. Two dynamic simulations were run to ensure that the process configuration would work successfully.
The implementation of a front-end NGL recovery unit brought the advantages of higher liquefaction pressure, better tolerance to lean gas, and early refrigerant production. "These advantages work to increase the overall efficiency of the system," Bladanet explained.
Construction plan. Achievements for the construction of Yamal LNG include the fabrication of 142 modules in just three years, and the continuation of construction activities involving 23,500 people throughout the frigid winter months.
However, logistical challenges were present in the shipping of modules from fabrication yards to the project site. At 103 m long, the longest modularized building the world was moved for the project. The heaviest module weighed 7,200 metric tons.
Commissioning and startup. The first LNG cargo was sent in December 2017, one year before the final performance tests were successfully carried out and the plant became fully operational. During this time, all three trains were started up—an impressive achievement for this far north LNG terminal.
Continuous operation above 100% has been observed since full operations were achieved, and partial production has been maintained above 26°C. Also, an enhanced throughput program takes advantage of colder months of the year to increase LNG production, Bladanet explained.
At present, TechnipFMC is conducting studies at the request of the operator to see how far production can be pushed, and so it is verifying the mechanical integrity of the plant.
"It's very likely that next year, between October and March, the project will be producing even more LNG," Bladanet said.
The GPA Europe Spring Conference is taking place at the Shell Technology Center in Amsterdam, the Netherlands, from 15–17 May.
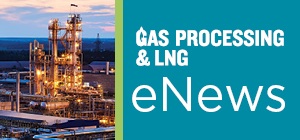
- ADNOC Gas awards $2.1 B in contracts to enhance LNG supply infrastructure
- U.S. Department of the Treasury releases final rules for clean hydrogen production tax credit
- Topsoe, Aramco sign JDA to advance low-carbon hydrogen solutions using eREACT™
- Nicor Gas celebrates its first renewable natural gas interconnection
- Phillips 66 outlines nearly $3-B capital program for 2025
Comments