GEA delivers for BP gas plant in Egypt
GEA has delivered two centrifuges for monoethylene glycol (MEG) purification at BP’s West Nile Delta offshore natural gas field in Egypt. The project represents an important new customer for GEA in its expanding MEG treatment business. MEG is used to protect gas pipelines from corrosion and blockage.
The centrifuge package was delivered to BP’s gas treatment plant near the port of Alexandria. Its two WSD 200 centrifugal separators run in parallel 24 hours a day to deliver excellent separation performance and reliable operation on a single skid measuring 12 x 7 x 6 meters.
Overcoming challenges to deliver on schedule
GEA started work on the project at the end of 2015 and supplied the centrifuges on schedule in around 65 weeks.
The complete MEG regeneration project was handled by the Wellstream Processing group, which is part of the Process and Flow Technologies business unit within National Oilwell Varco, L.P. (NOV). NOV’s head office is in Houston, Texas, USA. This is GEA’s fourth project with NOV, on this occasion working with the company’s office in Oslo, Norway. “The GEA centrifuge technology in the NOV MEG Regenerations Units has been subject to varying process conditions, interfaces and client requirements,” said Bruno Sersante, Senior Mechanical Engineer, Wellstream Processing group. “We have seen how a very well prepared GEA team has been capable of delivering a complex package on a tight schedule and with a high-quality standard. Their open approach has helped us to successfully meet the challenges set by our client along the way. NOV appreciates the proactivity and flexibility of the GEA team in meeting every challenge for the successful execution and delivery of projects on time and in budget.”
Jan Hoppe, Senior Project Manager GEA, agrees that good collaboration played a big part in this success. “I think we won the contract on our relationships with the project partners, our track record in handling projects of this size, and the technical performance of the WSD 200 centrifuges,” he says. “This was a challenging project, but we kept to the schedule and it was a fantastic effort.” Centrifuge manufacturing and project management were done at GEA’s facility in Oelde, Germany. GEA’s Dubai office assisted with front-line contact. The centrifuge skid was assembled in Hereford, UK, by KGD, a trusted partner of GEA.
West Nile Delta: a strategic project
The West Nile Delta is a strategic project that will eventually supply almost 1.3 billion cubic feet a day (bcf/d) of gas, equivalent to about 30 per cent of Egypt’s current production. All this gas will feed into the Egyptian grid.
The complete development consists of five gas fields in water depths up to 750 m. BP holds an 83 percent stake, with the balance owned by German oil and gas company DEA AG. Production started in March 2017, with the remaining fields expected on stream in 2019.
MEG protects pipelines
As well as natural gas, wellhead pipelines typically transport hydrocarbon liquids (condensate), water, corrosive salts, and sand. Within the pipeline there is a constant threat of erosion, corrosion and scale formation.
Subsea pipelines operating at temperatures close to freezing also risk plugging with hydrates. These ice-like substances form when natural gas – methane – combines with water at low temperatures.
MEG has a long history as an antifreeze in engines. Spraying MEG into pipelines binds condensate, water, salt, and corrosion particles, and stops ice and hydrates forming.
Recovering and purifying MEG
On the West Nile Delta project, MEG purified by GEA’s equipment protects a 42-km pipeline carrying gas ashore from nine wells in the Taurus and Libra fields.
Once the gas reaches the processing plant the MEG is recovered and purified for re-use. The GEA centrifuges are an integral part of the NOV pre-treatment system, where they remove precipitated low-solubility salts and fines from the rich MEG. Subsequent purification steps include reconcentration and salt reclamation.
GEA makes a range of centrifuges for MEG purification. For smaller projects the group offers several models in its WSE series. GEA’s largest MEG centrifuge, as used in the West Nile Delta project, is the WSD 200. This self-cleaning centrifugal separator has a direct drive, which yields maximum flexibility within a compact footprint.
All GEA MEG centrifuges provide the high g-forces required for good separation efficiency. Contact parts are made from super-duplex steel for maximum corrosion resistance. MEG centrifuges systems are also typically blanketed with nitrogen for safe operation in the presence of flammable gas.
A typical skid-mounted centrifuge package includes a separator, control panel, heating system, sludge tank, and sludge pump.
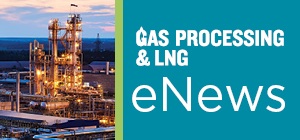
- ADNOC Gas awards $2.1 B in contracts to enhance LNG supply infrastructure
- U.S. Department of the Treasury releases final rules for clean hydrogen production tax credit
- Topsoe, Aramco sign JDA to advance low-carbon hydrogen solutions using eREACT™
- Nicor Gas celebrates its first renewable natural gas interconnection
- Phillips 66 outlines nearly $3-B capital program for 2025
Comments