Gastech ’15: Industry leaders explain why FLNG success starts with design
By ADRIENNE BLUME
Editor
SINGAPORE -- At Thursday afternoon’s special focus stream on FLNG innovation, containment and storage, Ian Jewitt, FLNG HSSE Team Lead for Shell Global Solutions, discussed floating LNG (FLNG) engineering in a safety context.
Jewitt explained how Shell has carried out exhaustive risk assessment studies for its Prelude FLNG project. These assessments included hazard identification exercises; quantitative risk assessments; fire, explosion and cold spill risk assessments; and ship collision studies, among many others.
Hazard identification. Due to the unique requirements of FLNG vessels, a number of potential hazards must be addressed. These hazards include hydrocarbons under pressure, loss of containment, boiler explosions and weather conditions, among many others.
“To understand the risks associated with all aspects of FLNG projects, it has been necessary to perform a full range of safety studies,” Jewitt said. “The layout of the entire facility was based on risk management."
Along these lines, heavy equipment is separated from personnel living quarters by as much distance as possible to minimize injuries or loss of life from potential fires and explosions.
Safety gap design and spill risks. Prelude’s safety design employs a safety gap philosophy, wherein large safety gaps are implemented between modules. These safety gaps act as mitigation gaps to reduce the risk of incident escalation.
Another area of concern is cryogenic spill risk. The risk of cryogenic spills is larger on an LNG carrier because of the additional process equipment needed on a floating LNG facility. Shell’s FLNG design minimizes the cryogenic inventory that could potentially be released, reducing the potential contact time of cold liquid spills within critical structures.
Viability of nearshore FLNG. Following Jewitt’s talk, Javid Talib, Vice President and FLNG Program Manager for Black & Veatch, examined the factors that make nearshore mid-scale FLNG a viable option.
As an alternative to building a fixed-asset,onshore plant, nearshore FLNG has a shorter construction schedule and can move to commercial operation much faster than a traditional FLNG project. “There’s a need to start conceptual studies right up front,” Talib said. “It’s never too early to start planning.”
Topsides and onshore planning. Design of the topsides begins with technology selection and decisions on production capacity, train sizes and LNG offloading strategy. Project planners must choose between a single large production train and multiple small production trains. A large single train provides economies of scale and a reduced footprint, but no operational flexibility and complex startup and turndown issues.
Conversely, the loss of economies of scale found with small multiple trains can be overcome with technology. Small multiple trains have an increased footprint, although the units can be modularized. A multiple-train configuration also yields operational flexibility, easier startup and shutdown, higher availability, dedicated trains for offtake, and production continuation during shutdowns.
The VP also noted that the CAPEX for nearshore mid-size FLNG projects is manageable, relatively speaking. “The CAPEX is bite-sized and bankable compared to other, larger FLNGs,” he concluded.
Gastech 2015 continues through Friday in Singapore. As the official conference newspaper provider, stick with Gas Processing for continued live coverage from the event.
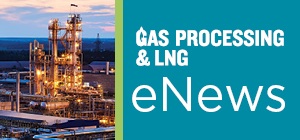
- Gasum powers Equinor's platform supply vessel with bio-LNG
- ADNOC deploys pioneering AI-enabled process optimization technology
- Mexico Pacific announces long-term LNG SPA with POSCO International
- ONEOK to acquire Medallion and controlling interest in EnLink for $5.9 B
- Golar LNG signs EPC deal for $2.2-B MK II FLNG conversion project
Comments