OTC ’15: Top Aramco engineer outlines trailblazing gas technologies
By Adrienne Blume
Managing Editor
HOUSTON -- The annual Offshore Technology Conference (OTC) opened on Tuesday with a topical breakfast on unique technical solutions to complex gas development projects.
Barbara Thompson of Aker Solutions introduced Saudi Aramco's Nabilah Al-Tunisi, Saudi Aramco's chief engineer. Al-Tunisi has worked with the company for more than 32 years.
In her talk, Al-Tunisi discussed the history, scope and challenges of complex gas field systems completed by Aramco in the Arabian Gulf.
The Arabiyah-Hasbah development contains 13 offshore platforms with a capacity of 350 MMscfd each. Gas is gathered through trunklines and transported to the Wasit onshore gas plant, which has a capacity of 2.5 Bcf.
Aramco was tasked with finding technical solutions for several challenges during the course of the project, Al-Tunisi explained.
These challenges included multiple sources of power both onshore and offshore, long distances traversed by trunklines, high pressures and temperatures, non-traditional wellheads, hydrate formation and corrosion, the presence of elemental sulfur, unconventional flare requirements and a demanding project time line.
Trunkline challenges. The Arabiyah-Hasbah wells are rated at a pressure of 15,000 psi and have an internal-diameter casing of 14 in. Additionally, a flow assurance analysis indicated that the temperature of the reservoir was likely to exceed 200°F and gradually decrease to below 120°F after a distance of 20 km.
Since the Arabiyah-Hasbah fields are located 150 km from shore, they required very long offshore trunklines with a 36-in. diameter. The lines also required long offshore composite submarine power cables.
During the design process, Aramco needed to change the ASME rating of the trunklines from 900 to 1500, and it needed to alter the trunkline thickness from 1.125 to 1.25.
"Basically, we had to update the entire system," Al-Tunisi said.
Unconventional flare system. The chief engineer also explained how Aramco decided on a high-integrity protection system (HIPS) in lieu of a traditional flare.
A traditional flare system would have introduced safety, technical and environmental risks due to the high pressure of the reservoir.
However, the HIPS, which is rated safety-integrated system (SIS) Level 3, enabled rapid opening and closing of the flare and was compatible with high pressures and temperatures.
The HIPS prevents overpressure of the platform by shutting off the source of high pressure before the design pressure of the system is surpassed. The systems were installed at all 13 wellheads, preventing equipment exposure to the higher pressures of the reservoir.
With HIPS, the required height of the flare tower is 80 m, as opposed to 100 m with a conventional flare. Also, the bridge length from each platform is 115 m with a HIPS, vs. 660 m with a traditional flare.
The systems are skid-mounted on two skids and feature 1.4-sec gate valve closures.
Power and solvent solutions. Aramco also utilized a static synchronous compensator (STATCOM) as a power source. STATCOM is a reliable voltage compensator system that is commonly used in the aviation industry, Al-Tunisi explained.
STATCOM is designed to regulate voltage variations using electronic controllers, with no mechanical switching. Two STATCOM units were installed on each platform.
The platforms also required elemental sulfur solvent-injection facilities to prevent hydrate formation. Monoethylene glycol (MEG) was both injected and recovered, a new technology application for Aramco.
Also, the Hasbah field's temperature and pressure conditions around the choke valves were found to be thermodynamically favorable for elemental sulfur deposition in the pipelines. Sulfur solvent injection was used to mitigate the effects of elemental sulfur deposition.
An injection quill was used to ensure that the solvent reached an ideal mixture.
Additionally, all of the wellheads had to be cladded with corrosion-resistant alloys, which was a costly and time-consuming process. "There was a lot of learning we had to do," Al-Tunisi acknowledged.
An ambitious path. The capital program's time line of three years was a demanding one, due to complex engineering and procurement delays. "There were continuous changes of process data during detailed engineering and procurement," Al-Tunisi said.
Contract work was expedited with the help of third parties, and multiple locations were used for fabrication. Three-dimensional modeling was used extensively during the fabrication process.
No other references existed for such high-pressure, high-temperature gas wells offshore, Al-Tunisi explained. This forced Aramco to forge a technology pathway to enable the safe, reliable production and gathering of gas from the Arabiyah-Hasbah fields.
OTC 2015 is taking place at the NRG Center in Houston from May 4–7.
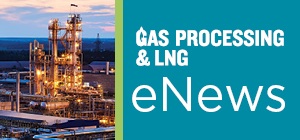
- Gasum powers Equinor's platform supply vessel with bio-LNG
- ADNOC deploys pioneering AI-enabled process optimization technology
- Mexico Pacific announces long-term LNG SPA with POSCO International
- ONEOK to acquire Medallion and controlling interest in EnLink for $5.9 B
- Golar LNG signs EPC deal for $2.2-B MK II FLNG conversion project
Comments